PU – Sustainability: A Step Towards a Sustainable Future
- ial
- Feb 20
- 5 min read
The global plastics and polymer market was estimated to account for around 460 million tonnes in 2024, and a considerable share of this ends up in the environment as pollutants in the form of waste and landfill. It has become a global necessity to move towards more sustainable, bio-based, bio-degradable and recycling centered approaches.
Polyurethanes (PU), being the sixth most produced and used polymer globally with an annual production of around 25 million tonnes, are facing challenges regarding production, recycling and end-of-life disposal. PU products are majorly thermosets, as about 52% of global PU products are produced as foams (flexible and rigid), and the rest are used in CASE (coatings, adhesives, sealants and elastomers) and binders; this makes their recycling and disposal very complicated.
The production of PU also causes significant environmental harms, hazards and emissions because of their dependency on petrochemical precursors and raw materials. The end-of-life scenario for the majority of PU includes equal shares of landfill and incineration, leaving a rather small share being reused or recycled.
To tackle these problems many global PU stakeholders are involved in extensive research and innovation efforts to develop sustainable and environmentally friendly solutions for the PU value chain. Two major focus areas for this are:
1) To produce more bio-based, easily biodegradable products by replacing the current fossil-based raw materials, which in this case are mostly isocyanates and polyols, with their bio-based or recycled variants.
2) To effectively recycle the discarded and degraded PU waste using chemical and physical recycling methods.
The traditional isocyanates like MDI, TDI, HMDI, etc., are made up of precursors such as toluene, aniline and benzene, which are converted into isocyanates using phosgene; this is a hazardous gas, and the process involves considerable greenhouse emissions and environmental hazards. New bio-based isocyanates and non-phosgene routes are developing steadily to curb the harmful effects and make the process eco-friendlier. Bio-based isocyanates using natural oils, lignin, amino acids, algae, saccharides and cashew nutshell oil, to name a few, are available in the market.
The bio-based content in the products is measured using the mass balance approach, allowing manufacturers to attribute the final isocyanate product as bio-based even though the renewable feedstock is mixed with traditional fossil-based feedstock.
Mass balance is a sustainable approach that combines fossil and alternative feedstocks in polyurethane production, reducing the carbon footprint by 60-70%. Major manufacturers like BASF, Huntsman, Evonik and Covestro now have portfolios of mass balance certified isocyanates in their ranges.
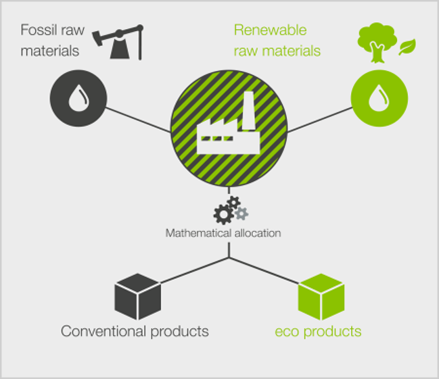
The mass balance approach
Similarly, bio-based polyols are also manufactured using many similar feedstocks to isocyanates, but natural oil polyols are the most prevalent ones. Polyols based on a range of vegetable oils - soya, castor, palm and rapeseed - are readily available in the market, especially in the Europe and Americas regions. However, natural oils also face competition from other sources of ‘natural’ polyols, such as those made from sugars (sorbitol and sucrose), or from bio-based diols and diacids, including bio-succinic acid.
In the polyurethane industry, natural oil polymers (NOPs) are used in flexible and rigid foams (furnishings and insulation, respectively), elastomers, sealants, paints and coatings. However, consumption levels are still small in Western Europe, and virtually negligible in Eastern Europe and the Middle East. Raw material producers in Europe seem to have a propensity for recycled and CO2-based polyols, as opposed to NOPs.
In Asia Pacific (APAC), NOPs based on soybean, castor and palm oil account for the largest proportion of sustainable polyols due to the abundant vegetable oil feedstocks available in the region. Competing bio-polyol technologies include those based on sugars and bio-based diols like 1,3-propanediol (PDO) and 1,4-butanediol (BDO) and diacids like succinic acid. NOPs have attracted attention from the polyurethane industry as a greener alternative to synthetic polyols due to the cost savings incurred when importing petroleum-derived polyols.
In China, bio-based polyurethane foam has struggled to gain market share due to its lack of price advantage and custom requests. Domestic suppliers struggle to provide consistent quality products, and there is limited consumption of soybean oil polyols in the country. There are still limitations on the use of bio-based polyols due to difficulties encountered in their incorporation into urethane formulations. Levels above the established limits typically lead to poor foam compression, poor stability, higher risk of tearing, and an undesirable odour.
Polyols from bio-based feedstock such as soybean oil, linseed oil, castor oil and cashew nutshell oil are being produced in North America. These polyols are used in automotive interior components, spray polyurethane foam, flexible PU foam slabstock, elastomers, carpet backing, and footwear components.
The contribution of NOPs to the overall polyols used for PU production was around 3% in 2024, and it is expected to increase its share to 12% up to 2032 under standard scenarios.
Being the largest market, flexible foam offers the largest overall potential for NOPs. In the paints and coatings segment, NOPs can be used in solvent-based acrylic and polyester systems to lower VOCs and increase the amount of solid content. Instead, in elastomers, the demand for bio-based TPUs is mainly driven by the sports footwear and medical device industries.
The concept of going green is becoming increasingly attractive as a business strategy, with most polyol companies offering bio-polyol products in their portfolios. However, customers are reluctant to pay the premium price for NOP-derived products, which can be three to four times higher than conventional polyols and lead to processing issues.
The second stage of the sustainable PU initiative is effective recycling of PU foams. Mechanical recycling is the easiest option for the recycling of polyurethane. For this process the foam is reduced to flocks and used for other end uses, such as carpet backing, NVH foam and acoustic insulation (known as bonded foam); however, this demand is relatively low compared to standard slabstock foam, and a considerable amount of waste is still accumulated. This kind of recycling is called open-loop recycling because it cannot be used to produce new products, but it is a good option when closed-loop recycling is not possible.
On the other hand, closed-loop recycling (CLR) is a sustainable approach to PU recycling, where materials are collected, processed and used to create new products without significant degradation in quality. This method minimises waste and maximises resource utilisation, making it the most sustainable approach to PU recycling.
In Europe, numerous institutes and companies are involved in research projects to find ways to reuse foam via chemical recycling. The technology has been in use at an industrial scale in Europe since 2013 for post-industrial waste and has now evolved to be able to recycle post-consumer foams. Several technologies for chemical recycling of PU foam are differentiated by the base material they use to dissolve the PU foam. Extended producer responsibility (EPR) schemes, e.g. for mattresses, can ensure that polyurethane material is available for recycling. Several industrial scale or pilot plants for chemical recycling of flexible polyurethane foam have been planned or are operational, notably in France, the Netherlands, Spain, Germany and Belgium.
Meanwhile, in the Americas there is growing interest in chemical recycling too, allowing reclaimed material to be reintroduced into the polyols. Several of the major PU raw material companies, including Covestro, Dow, BASF and Evonik, have already developed pilot facilities in Europe for the collection and chemical recycling of furniture and mattress foam, but activity in North America remains quite limited.
In the APAC region, closed-loop or chemical recycling is still at the R&D stage.
In summary, a combined effort of greener production techniques and effective recycling would make PU a much more sustainable polymer. Regionally, Europe and North America are the initial movers, with major technology advancements for bio-based raw materials and efficient chemical recycling; however, APAC being the largest producer, is also catching up. For the future, the need for waste management, environmental regulations and attempts to reduce fossil fuel dependence will be the major drivers for PU sustainability.
Source: IAL CONSULTANTS
Comentários